Full Paper View Go Back
Solving the Workshop Production Planning Problem Using the Meta-Heuristic Algorithm
M.J. Zangeneh Nejad1 , M. Mojarad2 , H. Arfaeinia3
Section:Research Paper, Product Type: Journal
Vol.8 ,
Issue.6 , pp.1-6, Dec-2020
Online published on Dec 31, 2020
Copyright © M.J. Zangeneh Nejad, M. Mojarad, H. Arfaeinia . This is an open access article distributed under the Creative Commons Attribution License, which permits unrestricted use, distribution, and reproduction in any medium, provided the original work is properly cited.
View this paper at Google Scholar | DPI Digital Library
How to Cite this Paper
- IEEE Citation
- MLA Citation
- APA Citation
- BibTex Citation
- RIS Citation
IEEE Style Citation: M.J. Zangeneh Nejad, M. Mojarad, H. Arfaeinia, “Solving the Workshop Production Planning Problem Using the Meta-Heuristic Algorithm,” International Journal of Scientific Research in Network Security and Communication, Vol.8, Issue.6, pp.1-6, 2020.
MLA Style Citation: M.J. Zangeneh Nejad, M. Mojarad, H. Arfaeinia "Solving the Workshop Production Planning Problem Using the Meta-Heuristic Algorithm." International Journal of Scientific Research in Network Security and Communication 8.6 (2020): 1-6.
APA Style Citation: M.J. Zangeneh Nejad, M. Mojarad, H. Arfaeinia, (2020). Solving the Workshop Production Planning Problem Using the Meta-Heuristic Algorithm. International Journal of Scientific Research in Network Security and Communication, 8(6), 1-6.
BibTex Style Citation:
@article{Nejad_2020,
author = {M.J. Zangeneh Nejad, M. Mojarad, H. Arfaeinia},
title = {Solving the Workshop Production Planning Problem Using the Meta-Heuristic Algorithm},
journal = {International Journal of Scientific Research in Network Security and Communication},
issue_date = {12 2020},
volume = {8},
Issue = {6},
month = {12},
year = {2020},
issn = {2347-2693},
pages = {1-6},
url = {https://www.isroset.org/journal/IJSRNSC/full_paper_view.php?paper_id=402},
publisher = {IJCSE, Indore, INDIA},
}
RIS Style Citation:
TY - JOUR
UR - https://www.isroset.org/journal/IJSRNSC/full_paper_view.php?paper_id=402
TI - Solving the Workshop Production Planning Problem Using the Meta-Heuristic Algorithm
T2 - International Journal of Scientific Research in Network Security and Communication
AU - M.J. Zangeneh Nejad, M. Mojarad, H. Arfaeinia
PY - 2020
DA - 2020/12/31
PB - IJCSE, Indore, INDIA
SP - 1-6
IS - 6
VL - 8
SN - 2347-2693
ER -

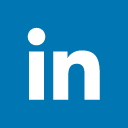


Abstract :
Workshop (cellular) production systems are one of the applications of group technology in industry, the purpose of which is to benefit from the physical or operational similarity of products in various aspects of manufacturing and design. Today, the use of workshop production systems and the use of its benefits as one of the ways to increase the speed of the organization`s response to rapid market changes, has received much attention. In this paper, a meta-heuristic algorithm based on a composition of genetic and greedy algorithms is used to optimize and evaluate the performance indicators of workshop production planning systems. To improve the effectiveness of the genetic algorithm, the initial population is generated by a greedy algorithm and several elite operators are used to improve the solutions. The greedy approach to improving the create an initial population prioritizes the cells and tasks in each cell and produces quality solutions accordingly. In order to evaluate performance quality of the proposed method, the P-FJSP dataset and quality, scatter, distance and time indices in a multi-objective function have been used. The experimental results show better performance of the proposed approach compared to NRGA and NSGA-II algorithms.
Key-Words / Index Term :
Workshop Production Planning, Meta-Heuristic, Genetic Algorithm, Greedy Algorithm
References :
[1] Solimanpur, M., Vrat, P., & Shankar, R. A heuristic to minimize makespan of cell scheduling problem. International journal of production economics, Vol.88, No.3, pp.231-241, 2004.
[2] Li, Y., Li, X., & Gupta, J. N. Solving the multi-objective flowline manufacturing cell scheduling problem by hybrid harmony search. Expert Systems with Applications, Vol.42, No.3, pp.1409-1417, 2015.
[3] Knosala, R., & Wal, T. A production scheduling problem using genetic algorithm. Journal of Materials Processing Technology, Vol. 109, No. 1-2, pp.90-95, 2001.
[4] Engin, O., & Döyen, A. A new approach to solve hybrid flow shop scheduling problems by artificial immune system. Future generation computer systems, Vol. 20, No.6, pp.1083-1095, 2004.
[5] Yang, Y., Chen, Y., & Long, C. Flexible robotic manufacturing cell scheduling problem with multiple robots. International Journal of Production Research, Vol.54, No.22, pp.6768-6781, 2016.
[6] Zeng, C., Tang, J., & Yan, C. Job-shop cell-scheduling problem with inter-cell moves and automated guided vehicles. Journal of Intelligent Manufacturing, Vol.26, No.5, pp.845-859, 2015.
[7] Ghalehgolabi, M., & Rezaeipanah, A. Intrusion Detection System Using Genetic Algorithm and Data Mining Techniques Based on the Reduction. International Journal of Computer Applications Technology and Research, Vol.6, No.11, pp.461-466, 2017.
[8] Rezaeipanah, A., Matoori, S. S., & Ahmadi, G. A hybrid algorithm for the university course timetabling problem using the improved parallel genetic algorithm and local search. Applied Intelligence, pp.1-26, 2020.
[9] Rezaeipanah, A., Nazari, H., & Abdollahi, M. Reducing Energy Consumption in Wireless Sensor Networks Using a Routing Protocol Based on Multi-level Clustering and Genetic Algorithm, International Journal of Wireless and Microwave Technologies(IJWMT), Vol.3, No.1, pp.1-16, 2020.
[10] Johnson, S. M. Optimal two?and three?stage production schedules with setup times included. Naval research logistics quarterly, Vol.1, No.1, pp.61-68, 1954.
[11] Opitz, H. Influence of Vibrations on Tool Life and Surface Condition in Milling Operation. International Institution of Production Engineering Research, 1954.
[12] Lopez, L., Carter, M. W., & Gendreau, M. The hot strip mill production scheduling problem: A tabu search approach. European Journal of Operational Research,Vol.106, No.2-3, pp.317-335, 1998.
[13] Erenay, B., Suer, G. A., Huang, J., & Maddisetty, S. Comparison of layered cellular manufacturing system design approaches. Computers & Industrial Engineering, Vol.85, pp.346-358, 2015.
[14] Yazhi, L., Xiaoping, L. & Jatinder, N. G. Solving the multi-objective flowline manufacturing cell scheduling problem by hybrid harmony search. Expert Systems with Applications, Vol.42, No.3, pp.1409-1417, 2015.
[15] Kia, R., Kazemi, M., Gol, S. S., Tavakkoli-Moghaddam, R., & Khorrami, J. A mathematical model for assessing the effects of a lot splitting feature on a dynamic cellular manufacturing system. Production Engineering, pp. 1-17, 2017.
[16] Jadaan, O. A., Rajamani, L., & Rao, C. R. Non-dominated ranked genetic algorithm for solving constrained multi-objective optimization problems. Journal of Theoretical & Applied Information Technology, Vol.5, No.5, 2009.
[17] Ahmadi, E., Zandieh, M., Farrokh, M., & Emami, S. M. A multi objective optimization approach for flexible job shop scheduling problem under random machine breakdown by evolutionary algorithms. Computers & Operations Research, Vol.73, pp.56-66, 2016.
[18] Zitzler, E., Laumanns, M., & Thiele, L. Improving the strength Pareto evolutionary algorithm. Technical Report TIK-Report 103, Swiss Federal Institute of Technology Zurich (ETH), 2001.
[19] Brandimarte, P. Routing and scheduling in a flexible job shop by tabu search. Annals of Operations Research, Vol.41, No.3, pp.157–183, 1993.
[20] http://people.idsia.ch/~monaldo/fjsp.html. Last Visited on 10 December. 2020.
You do not have rights to view the full text article.
Please contact administration for subscription to Journal or individual article.
Mail us at ijsrnsc@gmail.com or view contact page for more details.